
CASE STUDY
Time Management
Problem
This supplier of luxury clockwork products had to cope with a chronic lack of responsiveness in the marketing of its new products. The catalogue is rich and the models manufactured in exclusive series.
The problem to be resolved was to reduce by 50% the production time between the creator’s design and the market launch of a product certified according to Swiss watchmaking standards.
How to achieve such a goal was very important, since several past changes and reorganizations had not produced the desired results.
Solution
From interviews with members of the management team, it became clear that we needed to involve employees and change the way to think about production. This new approach would make it possible to build something sustainable.
We used the “Quick Response” approach, inspired by the QRM (Quick Response Manufacturing) methodology. The latter is based on an approach aimed at one element above all: motion time. The hunt for "white space" (unnecessary time for the client) was opened and a cell organization was tested. The new organization is based on the full empowerment of a multi-skilled team and the radical evolution of the executive’s role as a "team coach."
Results
From the first experiments, we were able to observe spectacular reductions in time on problematic areas: from 30% to 90%.
The generalization to the entire product development process within the next 6 months, coupled with a new distribution of roles, resulted in a sustainable reduction of 35% on average, with a record 60% reduction.
The path to the 50% reduction is close, 12 months ahead of the schedule initially presented to the executive committee.
As a positive consequence of this approach over time, the customer service rate rose from 70% to 95%.
Are you facing a similar problem for your business? We have several solutions to suggest.
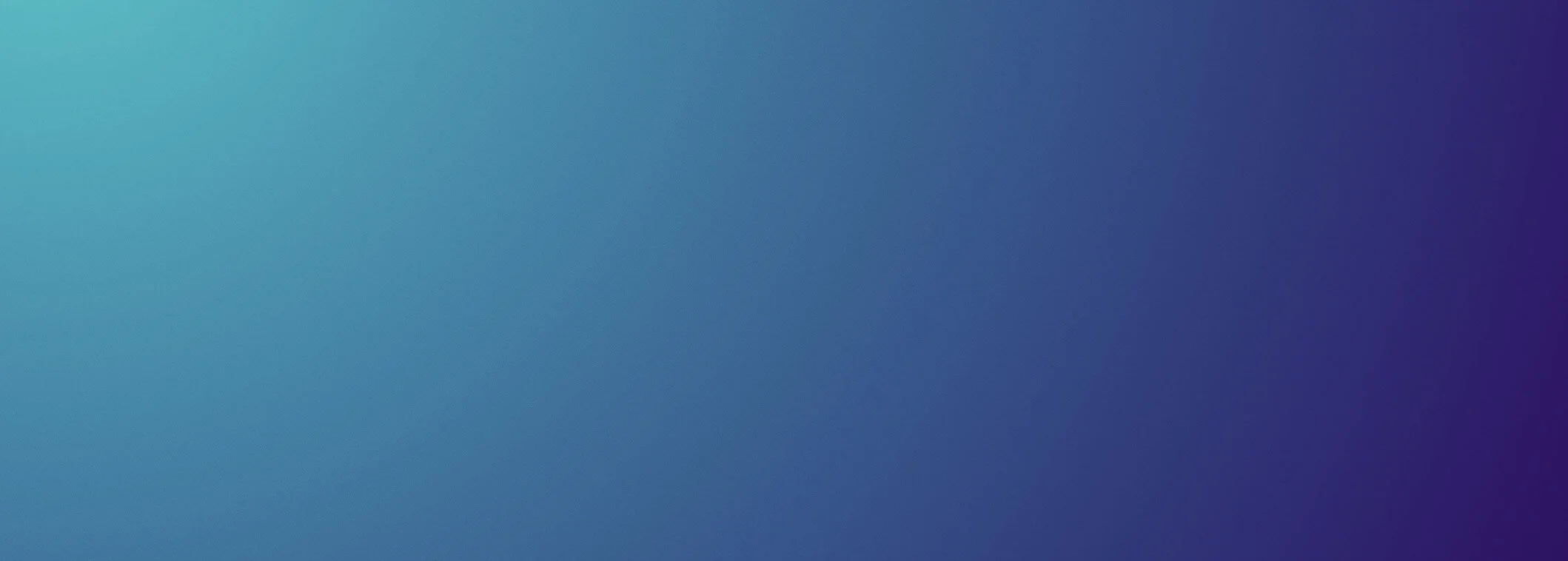
CASE STUDY
Process Optimization
Speeding up the time between online ordering and delivery becomes imperative in the face of the Amazon effect. This is what we did by optimizing a warehouse area of over 200,000 square feet and reviewing the packaging processes.